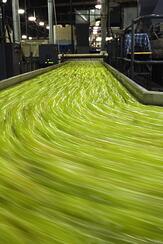
If you’re a food manufacturer with an eye on your bottom line, it’s time to take a look at where you may be sacrificing profit – starting with the quality of your rolls. Improper roll maintenance has the potential to damage your productivity and efficiency in a big way.
Frustrated by excess downtime, high energy use or loss of temperature control? Manufacturers in the food industry experience a number of recurring problems when using poorly maintained rolls. Implementing the right roll grinding and repair techniques is vital to addressing these issues.
Consider the following ways in which precision grinding services help improve your production process and maximize profitability.
1. Lowering Energy Use
Environmental consciousness is on the rise in the food industry. From organic options to responsible farming, consumers are showing that they care about these issues. Conserving energy is one way to make a positive contribution in this area. Even better, it boosts your bottom line with cost savings.
So, how do properly maintained rolls make this a reality?
For example, if you’ve got uneven, egg-shaped rolls in your manufacturing process, they’re going to vibrate within your machines’ bearings and gears, this will cause premature bearing and gear failure. Plus, your rolls’ spacial relationship changes, so the motor is constantly adjusting the amount of horsepower it applies. This is a real drain on energy – one that can be avoided with the right approach to roll maintenance.
Precision grinding ensures that your rolls run smoothly in the machine with a stable application of horsepower. When rolls are concentric and perfectly shaped, they don’t move out of place in the machine, so the motor doesn’t have to work as hard. This makes your manufacturing process much more energy efficient – and it puts more money back in your pocket.
2. Ensuring Tight Tolerances
Many roll grinding providers employ a process that involves grinding your rolls in place instead of removing them from the machine. But, this method does not focus on the shape of the individual roll, and that’s a mistake you don’t want to pay the price for.
Commercial roll grinders that rely on this method work only to ensure that the gap between the rolls is uniform, which typically results in very loose tolerances. Why should you be worried about this? Well, loose tolerances translate to:
- Lower efficiency
- Lower quality products
- More production issues
On the other hand, a provider that offers quality, precision grinding services is going to remove your rolls from the machine before grinding them. Only when the rolls are treated individually with precision services are they able to achieve a perfectly round shape.
What does it mean to say that “round” is important? At first glance, many rolls appear to be round after undergoing grinding services. But, the roundness of one end of the roll must be identical to the other, and the line running from the center of each end must be perfectly straight.
Without the correct shape, your rolls won’t run efficiently or produce a consistent product. In addition, you’re looking at extra time on unexpected maintenance and maybe even a shutdown. Manufacturers experience less machine downtime and a more uniform process when roll grinding is done the right way.
3. Controlling Temperature
Interior descaling and cleaning helps rolls maintain the correct temperatures. As the rolls run, they generate heat from the friction between the roll and the food product.
If you’re a manufacturer in the food industry, you probably know how frustrating it is to apply cooling water into a roll and not see the right temperature change. When materials coat the inside of a roll, the interior walls become thicker. High build-up makes it very difficult to cool the roll, which hinders the food manufacturing process.
To descale and clean a roll, your roll repair company must remove any of the following from inside the roll:
- Calcium build-up
- Lime
- Rust
- Other materials
Too much friction and heat could cause machine downtime – and that’s going to affect your productivity. Plus, high temperatures negatively impact the quality of your product. So, be sure to have your roll repair company clean and descale your rolls for better temperature control.
4. Achieving Greater Yield
Many manufacturers in the food industry use rolls to extract oil, process foods or create food products. Uniform rolls produce a more consistent product across the length of each roll, as the space between rolls is always constant. This results in a greater product yield.
Consider, also, the process of extracting oil from soybeans. Uneven rolls may be limiting how much oil your manufacturing process produces. Even if you sell what’s left of your soybeans as animal feed, this isn’t where your profits come from. Oil is much more valuable to consumers as a food product or ethanol gas.
Whether you are extracting oil or aiming for more uniform quality in your food production, you must have round, concentric rolls. Ensuring that your rolls are ground properly, descaled and cleaned has a powerful and positive impact on your bottom line.