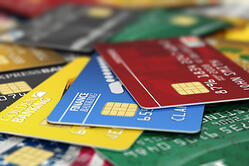
In the last year, massive security breaches compromising credit and debit card information have created a wave of new demand in the plastics manufacturing industry. Across just two large retailers – Target and The Home Depot – 96 million credit cards needed to be replaced. And one security breach on Black Friday led to demand for 40 million cards at once.
Such security breaches called for massive production of new cards, which deeply impacted you and may have compromised your production efficiency and quality. Moving forward, credit card innovations and new security measures are requiring greater quality demands in plastics manufacturing.
Meeting these higher precision standards requires precision roll grinding.
Increased Security With EMV Cards
A current standard in Europe and Canada, the United States is beginning to adopt the EMV (Europay, MasterCard and Visa) system. Also known as “chip and PIN” cards, this form of “plastic” is equipped with a microchip that contains the same information as the traditional magnetic strips and also requires a PIN. This technology is more difficult to copy and better combats the risk of fraud.
But because EMV cards are far from the standard in the United States, the rate of fraud in the U.S. has doubled over the last few years. Americans are simply easier targets for credit card fraud. But as Forbes notes, by the end of 2015, 70% and 41% of American credit and debit cards, respectively, will use security chips rather than magnetic strips. As a plastics manufacturer, it’s imperative that your product is uniform and enables your customers to produce these higher-quality products.
But how do you ensure product uniformity?
The Details Of Roll Grinding For The Plastics Industry
Rolls used in the plastic industry require extremely precise specifications. From shape and roundness to TIR, your roll grinding must be to 40 millionth of an inch or better to produce quality plastic. The roll defects are visible to the naked eye, which is not necessarily the case in rolls used in other industries.
But what might be most critical is that your roll grinder is using a method called 3D grinding. This technique accounts for the changing composition of your rolls when they are run under hot temperatures – typically 550 F. Because your rolls expand at such intense temperatures, and at different rates in different areas on your roll due to the metallurgy, the standard precision grinding process is not good enough.
In 3D grinding, your rolls are heated to their operating temperature and then put through the grinding process. The technique guarantees that when your rolls are subjected to production temperatures and have expanded, their tolerances are perfect and they are able to produce a consistent, high-quality product.