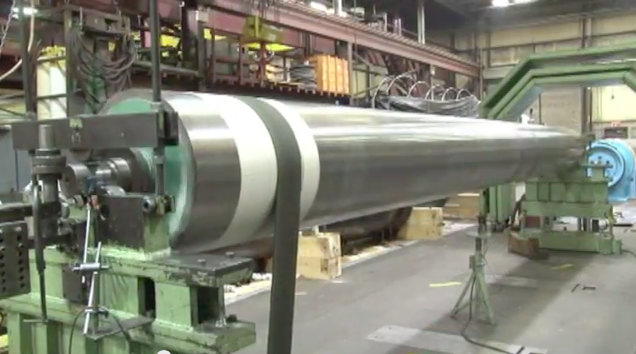
In PRG’s last blog post, we defined CNC systems and outlined how they’re used in precision grinding and other manufacturing processes. Roll grinding benefits from computer numerical control in a number of ways.
As a product manufacturer, the importance of your product’s consistency is second to none. The shape and caliper of your product must be consistent in order to maintain high quality, and the quality of your product directly impacts the quality of products your customers produce. Thanks to the increase in CNC grinding, your rolls are capable of being maintained to perfection – well beyond OEM specifications.
The Factors That Affect Quality And Efficiency
A CNC grinder offers you a number of manufacturing benefits, but there are three factors that go into producing a better product and maximizing your manufacturing efficiency.
Setup
The proper roll grinding setup is essential in fixing roll defects. With CNC systems and traditional grinding, proper procedure is to remove your roll’s bearings and housings. Without removing them, your roll has the potential to move during grinding, and the work fails to eliminate imperfections. In some cases, it may cause further imperfections in your rolls.
Environment
A proper, temperature-controlled environment is about consistency – it guarantees uniformity in the profile and dubbing of your rolls, and decreases thermal and mechanical deformation.
3D grinding, as it’s known, is crucial for rolls that are run at over 285 degrees F and those that are used for making products that need outstanding surface uniformity or minimal caliper variation.
Position
The positioning of the crown on your roll is as important to your manufacturing quality as its surface uniformity. By positioning the crown perfectly in the center of the roll, your TIR is within spec. But rolls that look perfect to the naked eye might produce poor-quality products, and the crown position is a common issue.
It would blow your mind how many roll grinding providers don’t get the crown in the exact center of your rolls.
The CNC Precision Grinding Standard
With the proper setup, environment and position, your rolls and manufacturing operations benefit from CNC grinding in invaluable ways. First and foremost, your rolls are ground to OEM specifications or better. Your roll is crowned perfectly, 360 degrees around. And, naturally, your roll’s crown is properly centered on the roll. Such roll precision is critical to your production quality, as machines are running far faster than originally designed, and any imperfection in your roll is magnified in your product and runability.
Surprisingly, CNC precision grinding is not yet a standard practice with roll grinding services. But, considering the many benefits it presents – largely pertaining to manufacturing efficiency and quality – businesses are smartly increasing its use. These manufacturers are reaping significant benefits and gaining a substantial advantage over those competitors that continue to grind rolls with imperfect processes.