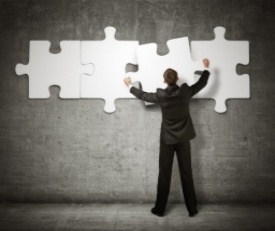
In any production environment, your main objective is to keep costs down and production efficiency up. This is especially true in the food industry, where you’re generating a large amount of raw materials every day.
If you’re a production manager in the food industry, there are often three major challenges you must overcome: lost yield, mounting energy costs and a lack of proper internal roll care. Find out how you’re able to solve these problems with proactive roll maintenance.
Lost Yield
When you begin your production process each day, one of your objectives is to maximize yield. You want to produce as much usable product as possible. To do so, you must be using rolls that meet your exact specifications.
This is especially true for processes in the food industry. Take soybean production, for example. Soybeans are run through rolls to extract their oils. To ensure you’re getting the highest yield from this process, the surfaces of your rolls must be uniform across their entire length and around the entire circumference.
With regular, proactive roll maintenance, your rolls are ground back to perfect concentricity and shape, with smooth surfaces that meet your specifications and enable you to prevent unusable yield.
High Energy Costs
There are a number of costs associated with the food industry, from production to shipping to worker employment. One cost you have the power to decrease is your energy bill. If your energy consumption is hurting your bottom line, look to roll maintenance as a solution.
When rolls are out of tolerance or uneven, they have to run longer to complete the same amount of work as concentric rolls. The gears and machinery within your rolls will wear and eventually start to vibrate, causing increased costs and energy consumption.
To ensure your rolls are using the minimum amount of energy, partner with roll grinding experts to return your rolls to perfect concentricity and shape. Round rolls run smoothly, stay in place and expend the least amount of energy.
Lack Of Temperature Control
With regular use, calcium, lime, rust, water and other materials build up inside your roll. When you fail to regularly clean and descale, these materials coat the inside of your rolls, thickening their walls. Higher build-up leads to poorer heat transfer in your rolls, causing a need to constantly pour water on them to decrease their temperature.
Food production is a science, and there are very specific environments that are conducive to successful production. When your rolls become too hot or too cool, your yield is at risk. However, proper cleaning and descaling during roll maintenance gives you more control over roll temperature.
In the food industry, rolls are critical factors affecting both your production and cost control. When you entrust regular cleaning and grinding to roll maintenance experts, you prolong the life of your rolls and keep production costs down.
Learn more about the costs associated with defective rolls in the food industry, and see how roll maintenance increases efficiency.