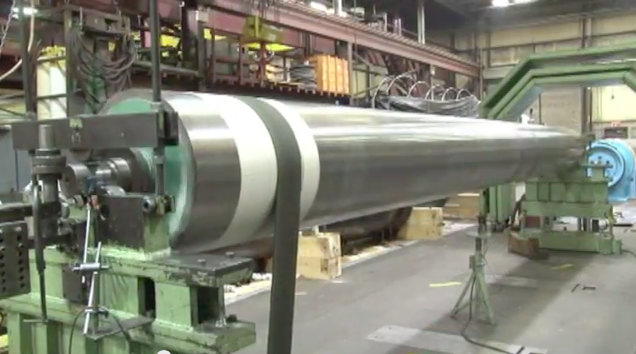
It doesn’t matter what type of manufacturing you’re in. Optimal production efficiency is a goal you should always strive for.
While there are certainly many variables impacting your efficiency that are out of your control, you must address those that you do have control over.
Take a step back to assess how you approach roll grinding and maintenance.
The 3 Biggest Issues From Ignoring Your Rolls
Without a proactive approach to monitoring your rolls, there are three critical issues that you’re bound to face:
1. Emergency shutdown
Few incidents are as costly to your business as a complete shutdown. Rolls that have been left unmonitored (or that have been poorly monitored) could create damage that forces you to shut down your production. In metals, for instance, your sheet could wrap around and damage your rolls.
2. Diminishing production efficiency
As your roll defects exacerbate, your production efficiency takes a hit. In many cases, manufacturers create reactive solutions to their problems. For instance, some paper manufacturers have added profiling equipment to fix moisture streaking from the press section. These press section rolls are often ground on an old worn out piece of equipment. This reactive solution doesn’t address the real issue of defective rolls, and it adds more time and cost to the production process.
3. Selling an unacceptable product that puts your reputation at risk
While an emergency shutdown is fairly unpredictable, eroding your product quality over time is not. In the paper industry, the use of the press section is one of the most economical methods of removing water from your sheet. Uneven and poorly ground press section rolls affect both sheet strength and uniformity. An irregularly ground roll produces an irregular sheet profile and, typically, irregular sheet properties for strength and other critical characteristics.
If you’re reacting to roll defects, there is no question you’ve already been putting out a sub-par product, and likely for some time. Given your customers’ expectations for high-quality sheets, you could be causing irreparable damage to your reputation.
Proactive, Precision Roll Grinding Is Essential
Mitigating the risk of product variability is imperative in all manufacturing industries. Not only does it help you maximize your production efficiency, but it also ensures the reliability and uniformity of your products – the backbone of sustainable success.
That’s why proactive, precision grinding is an absolute necessity.
What Does Proactive Roll Grinding Look Like?
Some manufacturers schedule roll grinding services in six- to 12-month increments. But, often, their rolls have already worn out.
Your rolls need to be changed based on a more logical decision-making process that’s dependent on how your rolls wear down. Many managers call this scheduling by the numbers.
Monitor your machine and product on your critical grades.
This may include:
- Degradation of your surface finish
- Lead test of calender rolls for barring, chatter, etc.
- Deviation from profile target of press section roll grind profiles
- Three-plane measurement of your press rolls to insure that the TIR, roundness and profile are in spec.
- TIR and shape of your rolls (make sure the range is only 5x the spec)
Press rolls with pressure sensors and printouts of your profile show if there is any deviation. It’s important to know why there’s deviation and how to fix it.
Companies used to monitor these critical metrics more frequently, but in an effort to become leaner, many laid off the team members responsible for such proactivity. In numerous cases, this has been a costly measure.
Remember, if you have to add chemicals, coatings or more costly fibers to hide defects in your product, you’re incurring an unnecessary cost for your production. Taking such a reactive measure may seem like the most economical decision on the surface, but it costs you far more in the long run.
Scheduled precision grinding increases the life of your rolls and helps you produce a higher-quality product that is uniform in machine and cross direction.
Stop cutting into your production efficiency, and make the necessary change in mindset to thwart the costly risks of reactivity.