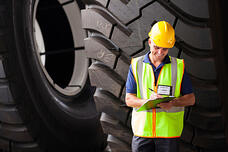
As the first month of the New Year comes to a close, an analysis of 2014 shows that plastic prices have declined while demand has improved. Why? Plastic manufacturers have been forced to battle profit loss, while the market has improved for consumers.
As Plastics Technology magazine explains, “Lower feedstock costs, improved availability of both feedstocks and resins with the conclusion of plant shutdowns (planned or not), along with a general improvement in demand, has brought about some price relief.”
The following table shows the range of plastic prices in 2014:
Plastic Prices (Per Pound) In 2014
- Polyethylene: $0.92 - $1.07
- Polypropylene: $0.76 - $0.79
- Polystyrene: $1.05 - $1.14
- PVC Resin: $0.77 - $0.80
- ABS: $0.94 - $0.97
- PC: $1.87 - $1.96
- Nylon 6: $1.51 - $1.65
- Nylon 66: $1.71 - $1.86
Over the course of the year, plastic prices have generally either leveled out and flattened or dropped. With these price effects and the pent-up demand for plastics, manufacturers have needed to add additional workers and costly equipment to meet their customers’ needs. This has led to an overall drop in profitability and production efficiency. In addition, plastic manufacturers now have fewer resources available to spend on innovation.
Other factors deeply impacting production quality, efficiency and profitability are increased machine speeds and improper roll grinding.
The increase in demand for plastic has led to increased machine speed. Running machines at greater speeds, however, increases the likelihood of your manufacturing efficiency and product quality taking a significant hit. At faster speeds than designed, your roll grinding must be absolutely precise – beyond OEM specifications. Shape, concentricity and roundness must frequently all be within one 40-millionth of an inch or better. With out-of-spec rolls, you’re bound to produce low-quality sheets – with defects that are more easily seen by the naked eye. In an oversaturated marketplace, quality is your biggest asset and greatest necessity.
Precision grinding in plastics manufacturing requires either 3D or hot grinding. These processes are vital because of the hot temperatures at which your rolls run. Under such heat (typically up to 550 degrees Fahrenheit), your rolls expand as the result of the metallurgy. However, the rate of expansion is not uniform across all areas on your rolls.
To account for the environment in which your machines and rolls run, hot grinding uses a method that heats your rolls to their operating temperature before beginning the roll grinding and measuring. This advanced method ensures that your rolls have perfect tolerances when actually used in your production process.
Without perfectly maintained rolls, your production quality and efficiency suffer. So, too, does your bottom line.